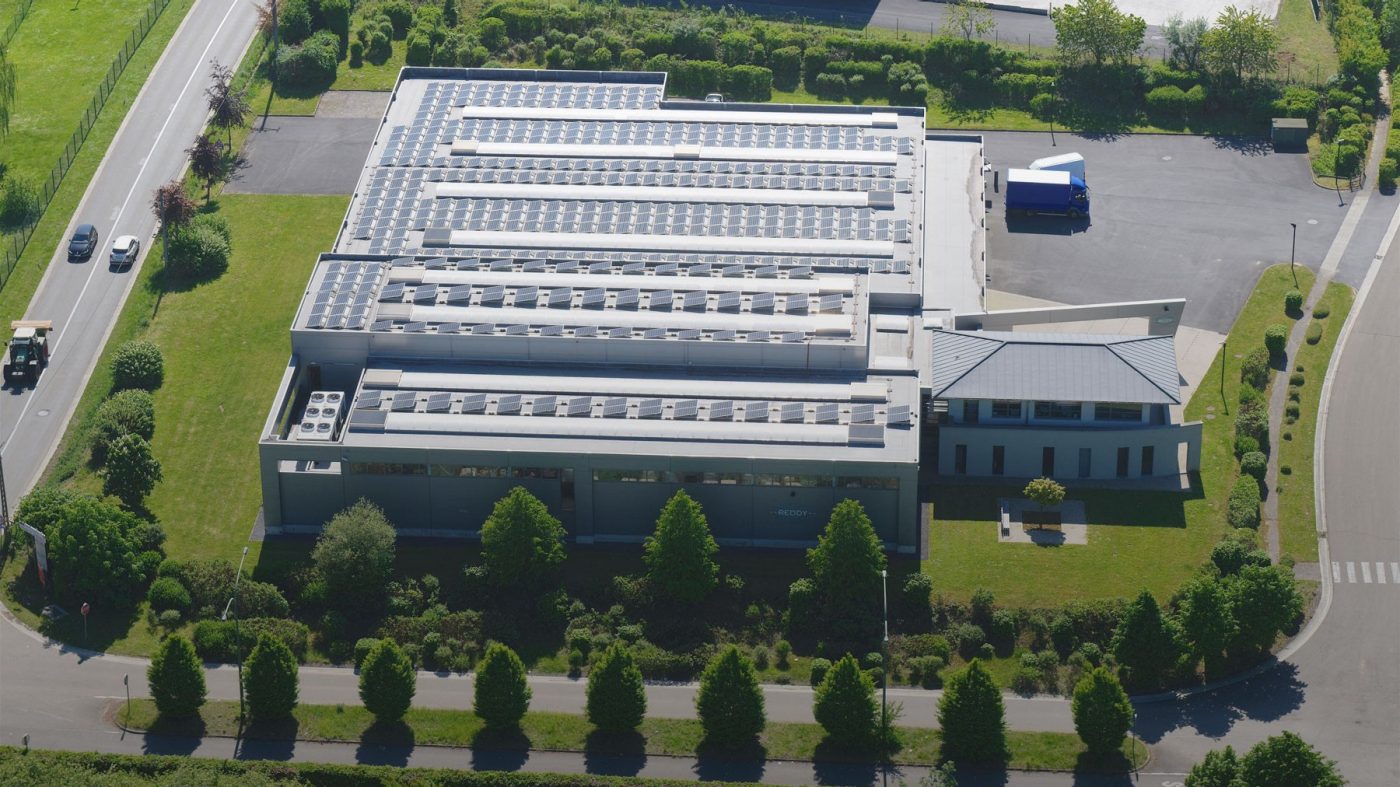
CO2-neutral through energy-efficient production
More than ten years’ energy-efficient production at Wienerberger’s Reddy subsidiary thanks to a modern heat pump system and solar cells on the factory roof.
More than ten years’ energy-efficient production at Wienerberger’s Reddy subsidiary thanks to a modern heat pump system and solar cells on the factory roof.
150 fewer tons of CO2 per year: That’s what Wienerberger’s subsidiary Reddy has achieved with its energy-efficient production processes. The stand-out characteristic of the new factory building constructed in 2009 in Seneffe in Belgium is the innovative heating and cooling system. This brought the previously separate processes together in a single circuit.
At its production plant in Seneffe in Wallonia, Reddy manufactures high-quality electrical accessories. The company is best known for its innovative, airtight wall boxes that meet the highest specifications in the fast-growing segment of energy-efficient buildings. To match these high standards in its own operations, the company developed and implemented a new innovative heating and cooling system for its production site. The production machines are cooled in a closed circuit.
A system of heat pumps extracts the heat which is used to produce hot water and heat the offices. The content of the 10,000-liter water-storage tank is kept at a constant temperature of 30 degrees Celsius. Reusing the hot water eliminates the need for additional gas or oil and reduces water consumption. “We developed this solution specifically for our own requirements. Today, we no longer generate any CO2-emissions from heating and cooling, and benefit from environmentally-friendly processes”, explains Christian Rouanet, General Manager at Reddy S.A.
“We developed this solution specifically for our own requirements. Today, we no longer generate any CO2-emissions from heating and cooling, and benefit from environmentally-friendly processes.”
In addition to the modern heat pump system, the company also prioritizes the use of clean electricity and for this purpose installed solar cells on the factory roof. These cells generate approximately 20 percent of the electricity required for production – in sunny months, the solar modules even deliver almost half the total electricity requirement.
Each year, the solar array produces 100,000 kilowatt hours (kWh) of electricity, the amount needed to run 100,000 cycles of a washing machine, make 7 million cups of coffee or prepare 100,000 lunches for four people on an electric cooker.
In addition to sustainable production processes, Reddy also uses recycled plastic. The scrap generated during the production of plastic items is cut into small pieces and then reused to make new products. “Our production is already carbon neutral thanks to our modern heating and cooling processes. As part of our drive towards greater sustainability, we will make even more use of recycled plastic in production in future”, says General Manager Christian Rouanet.
This environmentally-friendly method of production is also reflected in the products themselves. The airtight wall boxes in particular are a well-known Reddy S.A. product and in 2014 won the Belgian innovation prize Plastiwin. “The boxes prevent warm indoor air from escaping and cold outdoor air from entering a building, increasing its long-term energy efficiency”, says Rouanet.
“Our production is already carbon neutral thanks to our modern heating and cooling processes. As part of our drive towards greater sustainability, we will make even more use of recycled plastic in production in future.”
Reddy S.A. became part of the Wienerberger Group in 2019. The acquisition of the Belgian specialist manufacturer enlarged Wienerberger’s product portfolio in the highly attractive electro business. The integration of Reddy into the Wienerberger Piping Solutions Business Unit will leverage synergies in joint product and system development and stimulate growth by using Wienerberger’s strong distribution channels in its core markets.
Thus, Wienerberger now offers complete solutions for buildings as a single source supplier: from empty and pre-wired conduits, to installation boxes and accessories. Since the beginning of 2021, the products have been sold in Austria as well as in Belgium. Plans are now being drawn up to sell the products in other countries as well – including Germany, Norway and the Netherlands.