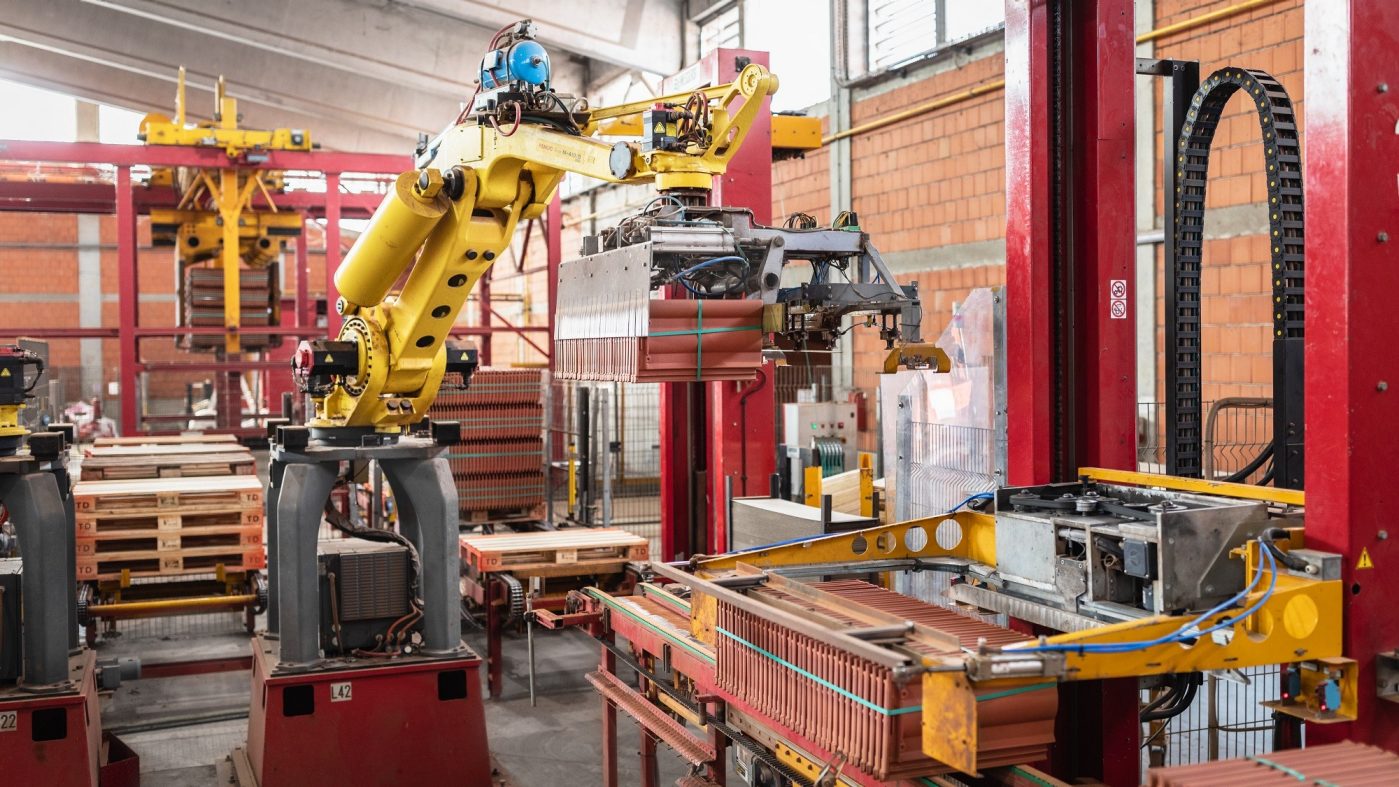
Three New Robots for the Roof Tile plant in Kanjiza
At the Kanjiza roof tile plant in Serbia, roof tiles are now efficiently stacked in cassettes with great precision by robots and unloaded again.
At the Kanjiza roof tile plant in Serbia, roof tiles are now efficiently stacked in cassettes with great precision by robots and unloaded again.
From artificial intelligence to automating production processes: Wienerberger has a strong focus on innovation and digitalization in its plants. This makes good business sense as it enhances efficiency and improves safety at the workplace. A good illustration is the automated loading and unloading of roof tiles by three robots at the northern Serbian plant in Kanjiza.
The refractory U-cassette (and the more commonly used H-cassette) is a piece of kiln furniture used for firing roof tiles. The unfired tiles are stacked upright next to each other in a U-shaped carrier that holds them together. For many years, each roof tile made at Wienerberger’s roof tile plant in Kanjiza was placed in a U-cassette on the kiln car and removed again by hand after firing. The tiles were then inspected, packed by hand and loaded onto pallets.
This repetitive work was physically demanding for the workforce. Safety standards at Wienerberger also increasingly presented a powerful argument against these manual processes. As a result, within just two months the plant was automated and now uses robots to load and unload the roof tiles.
Colorful interplay of green and yellow robots: This is how the robots work at Wienerberger’s plant in Kanjiza. The green robot picks up the roof tiles with its gripper and places them in the U-cassette. The metal fingers of the gripper open and close as the robot relentlessly stacks one tile after another in the cassette. After firing, two yellow robots then remove the products from the cassettes in preparation for the next stage. “What makes the robots used here so new and special is that they never stop: There is no other roof tile plant that has a process like it”, explains Lieven Sanders, Head of Technology – Roof at Wienerberger.
The robots know exactly where the U-cassette has to be placed in the kiln. It is suggested that further automated applications are conceivable in the future - from adjusting raw material quantities and kiln settings to automated quality control. “Automation is helping make processes and quality assurance ever more efficient. It should soon be possible, for example, to scan products on pallets to find out when they were manufactured,” says Sanders.
Automation is helping make processes and quality assurance ever more efficient. It should soon be possible, for example, to scan products on pallets to find out when they were manufactured.
Approximately 37.5 million roof tiles are produced each year at Kanjiza. Thanks to the robots, the plant can operate for longer and capacity can be increased at short notice. Work that used to be performed manually is now carried out by the robots. There is no downtime for breaks, product quality is higher, and less scrap is produced. “Thanks to the robots, we now need fewer employees for the actual production cycle which frees them up for other tasks, such as monitoring the processes,” says Sanders.
In addition, employees enjoy better safety and well-being as the elimination of repetitive work reduces muscle and joint pain. Since people are no longer in the vicinity of moving parts, safety on the shop floor has also increased. Now that processes are running smoothly, the team has more time to focus on optimization: One example is reducing the weight of the roof tiles which will further lower energy consumption and CO2-emissions.
The robots free up employees for other tasks, such as monitoring the processes.
There were also challenges to overcome when automating the processes, such as creating space for the robots in the limited area available. After the first few runs, the material used in the equipment had to be replaced so it could withstand the heavy-duty work without wearing out too quickly. “We took a risk by trying something completely new. But thanks to our highly motivated employees and with a little creativity, we were able to overcome initial difficulties and successfully implement a great project”, says Sanders.
Projects like the automated loading and unloading of roof tiles by robots are key steps for the future and safeguard Wienerberger's position as an innovation leader. The robots used here are particularly innovative with their ability to make so many controlled movements at high speed within a small area. This new capacity will be harnessed for use in future projects.