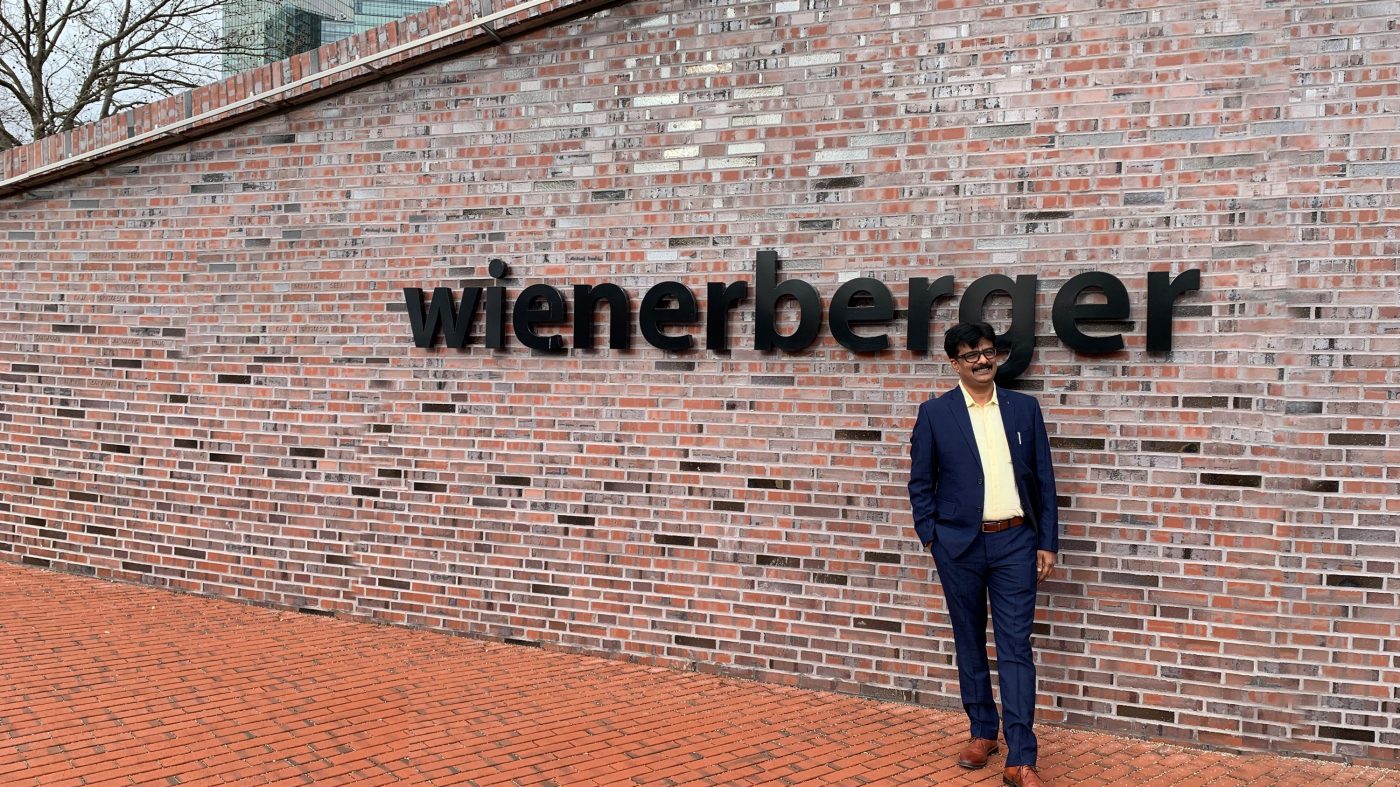
“Life-long Learning Broadens my Horizons”
Plant Manager Jagadeesha DJ knows living means learning and is honing his leadership skills on the wienerberger talent program Ready4Expertise 2.0.
Plant Manager Jagadeesha DJ knows living means learning and is honing his leadership skills on the wienerberger talent program Ready4Expertise 2.0.
Having obtained his Master’s degree in applied geology, Jagadeesha DJ was ready to follow his dream. The science postgraduate from southwest India entered the ceramics industry when he joined wienerberger India as a geologist 16 years ago. Today, Jagadeesha runs wienerberger’s Kunigal production plant in his home province, Karnataka. He is passionate about his work and still gets excited discovering new aspects to the job.
Head of Plant Operations Jagadeesha DJ on his experience with the Ready4Expertise 2.0 program and his career path at wienerberger.
wienerberger India produces 530 tons of brick per day at its plant approximately 70 kilometers west of Bengaluru, the capital of Karnataka state. This enormous output is down to Jagadeesha DJ and his team. How do they do it? “With seamless coordination and a good working atmosphere,” says the plant manager. As head of the fully automated production plant in Kunigal he is responsible for approximately 150 employees. “I am extremely proud of my resourceful and highly-motivated colleagues. I can rely on them completely.”
After eleven years as plant manager Jagadeesha loves his job more than ever. His top priority is the health and safety of all those who work for him. The 47-year-old generally starts work in the morning with a team meeting to get an overview of the day’s business. Topics on the agenda include production and maintenance, raw materials, energy, quality and sustainability: “With a relentless focus on reducing CO2 emissions, we are constantly working to make our processes even more sustainable.”
“I am extremely proud of my resourceful and highly-motivated colleagues. I can rely on them completely.”
Bright blue skies, palm trees and blazing sun – this is the setting of wienerberger’s first production site in Asia. wienerberger India began manufacturing Porotherm bricks in Kunigal in 2009. In addition to high safety standards and modern technology, the company has a strong focus on sustainability. For example, about 95 percent of the electrical energy used in plant operations comes from renewable sources. Quality assurance is carried out in a state-of-the-art laboratory and testing facility. Would you like to visit the factory? You can do so either in person or online:
In 2022 wienerberger launched Ready4Expertise 2.0, its group-wide talent program for experienced managers and experts. The program provides long-serving employees with proven track records vital input to enhance their professional development. Underpinned by the Go M.A.D. Results Framework®, managers learn to think and act differently, empowering them to coach their staff and improve results. These high performers are given support in formats such as webinars, regular check-ins and coaching. At the end of the program, they show off their skills in a pitch challenge at wienerberger headquarters.
The twelve members of the first Ready4Expertise 2.0 cohort come from ten different countries. One of them is Jagadeesha DJ. He is grateful to his boss for nominating him. But the reason he was accepted on to the nine-month-long program was that as plant manager he is a vital element of wienerberger India’s success. Ready4Expertise 2.0 let him develop his leadership qualities and get even more out of himself. His ambition now is to use teambuilding activities at his plant to strengthen team relationships among his colleagues.
“Jagadeesha DJ has been associated with wienerberger India since the inception of the company and has been instrumental in making our manufacturing unit in Kunigal one of the best performing amongst the wienerberger global blocks plants. He has the potential to take on more responsibilities. Hence the Ready4Expertise 2.0 program was a good platform for him to hone his leadership skills and also network with likeminded colleagues from the group, I have the confidence that Jagadeesha can achieve much more in his professional career and wish him all success.”
One of the things the family man appreciates most about the Ready4Expertise 2.0 program is the diversity of those taking part. “Sharing stories about our own experiences and also working together meant we were able to learn a great deal with and from each other.“ The program encourages him to look at situations from several angles. As he says, “In my work I set clear goals and execute them in a structured way. This includes how I make the best use of my peoples’ strengths, coach them and make decisions with them. This way, we can turn problems into solutions together,” says Jagadeesha DJ.
Jagadeesha DJ chose Lean Six Sigma Black Belt certification as his personal project for the Ready4Expertise 2.0 program. To earn the “black belt,” he had to demonstrate strong social skills in addition to professional expertise. The Ready4Expertise 2.0 program gave the plant manager the opportunity to broaden his skills. He now wants to use the knowledge he gained on the development program to achieve operational excellence and to further optimize production processes at wienerberger India.
In his spare time, Jagadeesha enjoys relaxing with his family. Even away from the office he indulges his love of strategy and learning by playing chess with his children or reading. The head of plant operations says that Ready4Expertise 2.0 has given him more confidence looking head: “My team and I have set our sights high. Ready4Expertise 2.0 was a great help finding the best way to go forward and achieve our goals and to approach the challenges we face with confidence.“ The more he learns, the more he realizes how much there is still to be learned.
“My team and I have set our sights high. Ready4Expertise 2.0 was a great help finding the best way to go forward and achieve our goals and to approach the challenges we face with confidence.“
Ready4Expertise 2.0 is one of three talent programs at wienerberger to support high-performing experienced managers and experts. The program lasts nine months and participants are nominated by their superiors. In addition, wienerberger offers the programs Ready2Grow and Ready4Excellence.