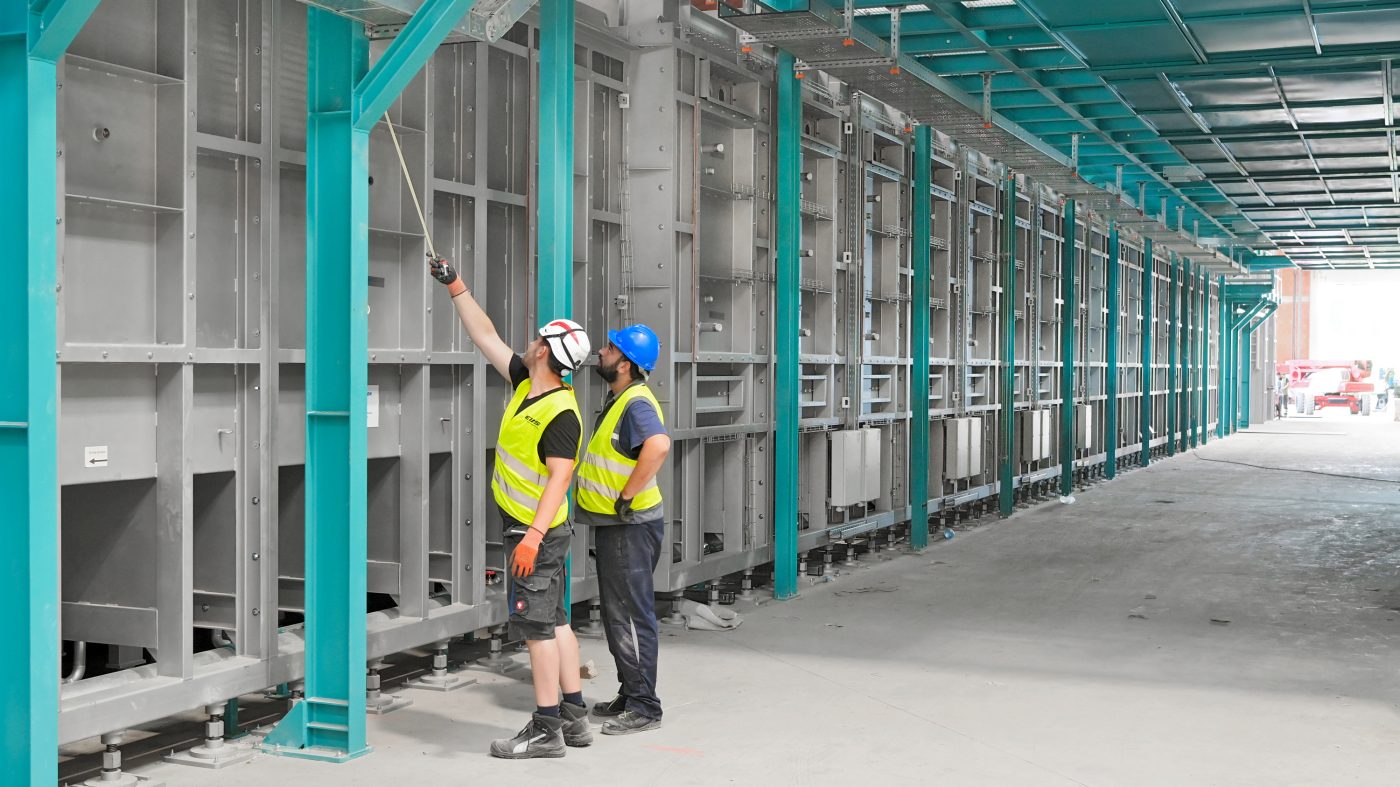
GreenBricks: Electric Kiln Revolutionizes Brick Production
Electric kiln, climate-friendly clay blend: wienerberger sets new standards in the decarbonization of brick production with a pioneering project in Austria.
Electric kiln, climate-friendly clay blend: wienerberger sets new standards in the decarbonization of brick production with a pioneering project in Austria.
The Upper Austrian plant in Uttendorf is a pioneer in the field of energy efficiency and the reduction of carbon emissions in brick production. As part of its GreenBricks project, wienerberger is developing and testing trailblazing solutions such as the world’s first electric kiln for clay blocks. What’s more, in the future, other locations will also benefit from the expertise gained and the technologies developed as wienerberger drives brick production toward climate neutrality.
The Green Deal aims to make Europe the first climate-neutral continent by 2050. wienerberger supports this vision, for example with its Sustainability Program 2026 and with projects to get the industry climate fit. One good example is the GreenBricks project at wienerberger Austria’s production plant in Uttendorf. The centerpiece of the project is the world’s first industrial-scale electric kiln for brick firing driven by green electricity. A similar technology – albeit on a significantly smaller scale – has been used successfully for the production of brick slips at wienerberger’s plant in Kortemark, Belgium, since 2020.
“Usually in the industry bricks are dried and fired in gas-fired dryers and kilns. At the demonstration plant in Uttendorf we are electrifying these processes, making them more energy efficient and relying completely on green electricity from renewable sources”, explains Johannes Rath, Chief Technology Officer, Ceramics & Concrete at wienerberger. This approach will reduce CO2-emissions from production by 90 percent in future and cut energy consumption by one third. The result is a flagship plant with almost carbon-neutral brick production.
“At the demonstration plant Uttendorf we are electrifying the drying and firing of bricks, making these processes more energy efficient and relying completely on green electricity from renewable sources.“
There is much more to the project though than the almost 90-meter-long, energy-efficient electric kiln. A significant aspect are improved clay mixtures: Aggregates such as coal or paper fibers have been replaced by more climate-friendly sawdust from a local sawmill that is then processed at the plant. The dryer has also been lengthened by 25 percent to improve energy efficiency. Furthermore, self-propelling vehicles have been introduced to transport the bricks during the production process. These automatic guided vehicles bring added flexibility to the manufacturing process and supply online product data to the process control system.
Three new heat pumps will be used to dry the bricks. The team at Uttendorf was already familiar with this technology since a compression high-temperature heat pump was taken into operation at the plant in a pioneering project in 2019. The photovoltaic system on the roof now also has twice as much power. The solar power supplements energy purchased from domestic hydropower suppliers. To transport the energy required for production, wienerberger laid a five-kilometer-long electric power line. Although some of the project was funded by the New Energy for Austria (NEFI) climate fund, wienerberger financed most of the ambitious project itself.
Aerial view of the electric kiln: The project relies on energy efficient firing technology and makes optimum use of the existing firing chamber to manufacture bricks.
A team of around 40 employees from the plant, local experts and personnel from wienerberger headquarters are responsible for the implementation of the GreenBricks project. Additional support is provided by research institutes and regional businesses. Project management is the responsibility of project manager Rene Pesendorfer from wienerberger and plant manager Gerhard Pichler from wienerberger Austria. “Having such a lean team enables us to make decisions quickly. And it means we are very agile for a project of this scale”, says Rene Pesendorfer.
“Together with the Austrian Institute of Technology (AIT) we developed a concept to make the kiln, dryer and heat pumps as energy efficient as possible”, says Johannes Rath. The calculations for the new furnace are based on a digital twin, in other words a virtual model, which uses high performance computing for thermodynamic simulations in order to optimize processes and equipment in advance.
“Having such a lean team enables us to make decisions quickly. And it means we are very agile for a project of this scale”
Electric kiln during construction: Years of planning and hard work have gone into the GreenBricks project for the carbon neutral production of bricks.
Planners and engineers have spent three years preparing for the GreenBricks project. Construction finally began in spring 2022 and in summer 2023 production in Uttendorf came to a halt. The project is also mindful of the circular economy: With the approval of the local authority, building materials from the demolition work were used as the roadbed material for the new access road to the plant. Most of the technical equipment belonging to the dismantled gas-fired kiln and the existing heat pump will be put back into service at other wienerberger sites.
Production in Uttendorf has been up and running again since fall 2024. The result: a first nearly carbon-neutral brick. The demonstration plant was inaugurated at the end of November and will be fully operational again in 2025. A particularly positive aspect is the broad-based support for the project among employees working at the site, at wienerberger Austria and beyond as well as among external partners. “I am delighted that our colleagues are so proud of this project. Some even come here specifically to see GreenBricks in action for themselves”, says Rene Pesendorfer. This enables additional sites to learn about the greenest brick production in Europe.
From left to right: Plant Manager Gerhard Pichler, Bernd Vogl (Managing Director Klima- und Energiefonds), Urban Peyker (Klima- und Energiefonds), LR Stefan Kaineder, Johannes Rath (CTO wienerberger), Gerhard Hanke (CFO wienerberger), Andreas Kugi (Managing Director AIT), LR Markus Achleitner, Johannes Manglberger (Mayor of Uttendorf), Gerhard Dell (State Energy Commissioner Upper Austria), Gabriele Egger (Deputy State Energy Commissioner Upper Austria), Johann Marchner (Managing Director wienerberger Austria).